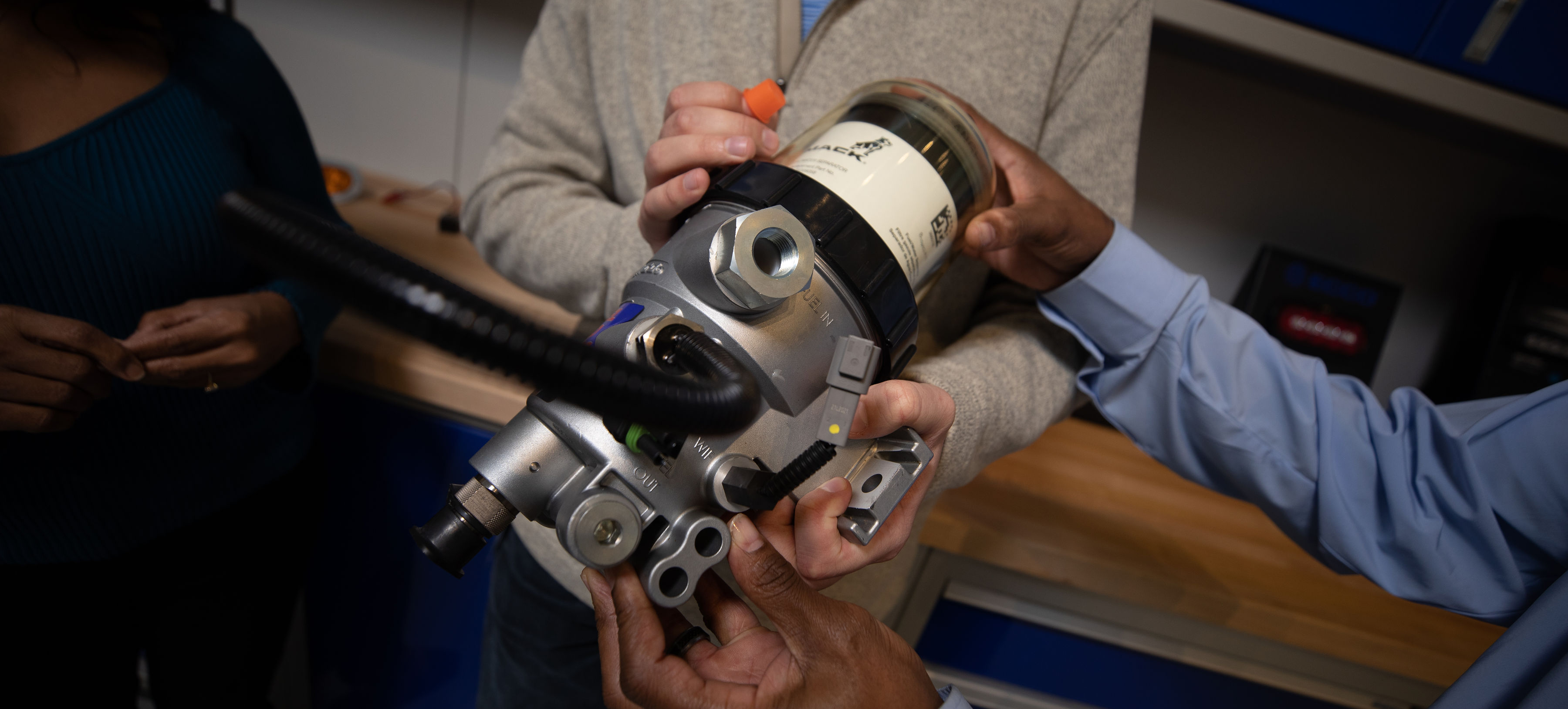
Diagnostics
DAVCO offers indepth support and information on all things diagnostic for diesel fuel filter and water separators. Review the literature below for detailed directions on everything from Air Bubbles to Heater Testing.
DISTINGUISHING AIR FROM VAPOR BUBBLES IN A DIESEL FUEL SYSTEM
Learn more about how to tell if you are experiencing air or vapor bubbles in your fuel system.
Diagnostics with the Clear Cover
How to tell if a fuel filter needs to be changed? Learn more about how to view the fuel level through the DAVCO patented Clear Cover.
FUEL QUALITY ISSUES
Having issues with your fuel quality? Know what to look for so you are able to react accurately andprotect your engine.
Leak Detection
Experiencing a leak? Learn more about the different types of leaks and how to fix them.
Heater Testing
Having an issue with a diesel fuel filter heater? Learn more about how to diagnose and treat.